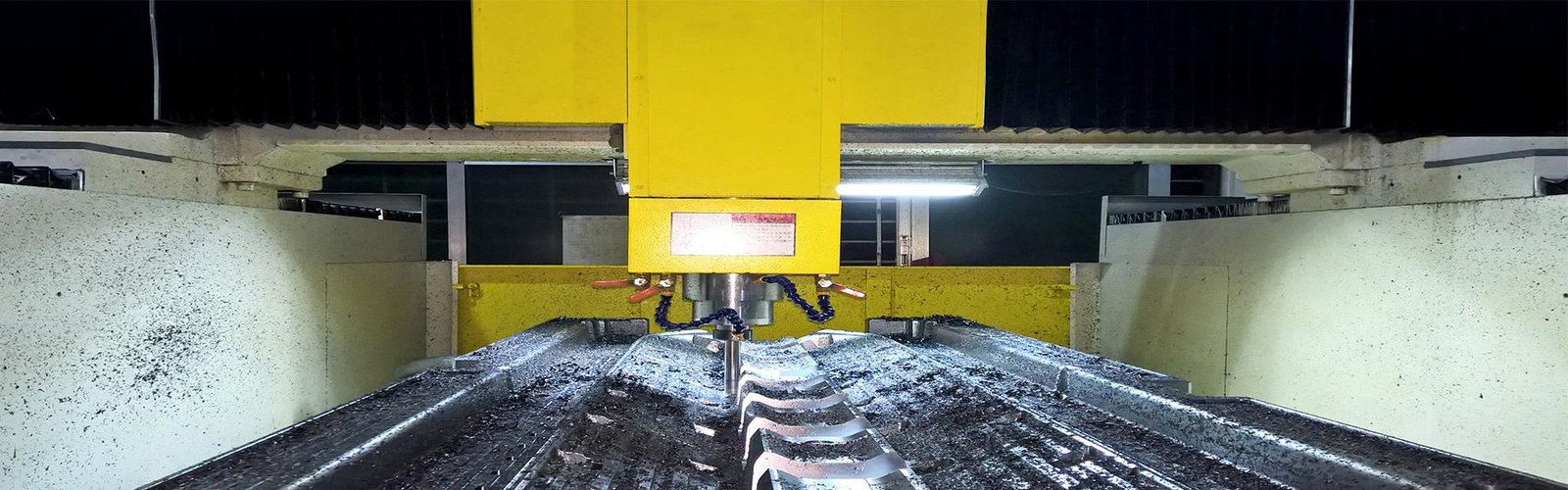
Study On Fire Resistance Of Ceramic Silicone Rubber Materials
The increase in requirements for fire-resistant standards and the soaring price of copper have made it increasingly difficult for traditional mica tape-wrapped mineral insulated cables and magnesium oxide cables (MI cables) to meet the market requirements for fire-resistant cables. The emergence of ceramized polymer refractories has made the development of fire-resistant cables a breakthrough.
The ceramized polymer material has the basic characteristics of ordinary plastic rubber under normal conditions, and rapidly becomes a hard ceramic-like casing in the event of fire or high temperature, and protects the power supply capability of the cable in a fire.
At present, ceramized silicone rubber and ceramized silicone rubber composite tape products have been widely used in various types and models of medium and low voltage wire and cable, creating enormous economic value and social contribution.
However, the use of ceramized silicone rubber materials requires special silicone rubber extrusion vulcanization equipment. Most of the wire and cable manufacturers do not have such equipment. The initial cost of new equipment is large; the use of ceramized silicone rubber composite belts has low production efficiency. The problem of high material cost. Therefore, the market is eager to call for the emergence of ceramic polyolefin refractories that can be produced using ordinary plastic wire extrusion equipment.
According to the experimental results, ceramized low-smoke halogen-free polyolefin refractories have been widely used in medium and low-voltage fire-resistant wire and cable fields due to their excellent fire resistance, good processing performance and low price, and have achieved good economic and social benefits. benefit. As a new type of ceramic polymer material, ceramized low-smoke halogen-free polyolefin refractory material will inevitably lead to a new revolution in the fire-resistant wire and cable industry.